Tư vấn - Srew compressor"TECHNICAL OIL-FREE" KHÔNG PHẢI LÀ KHÔNG DẦU
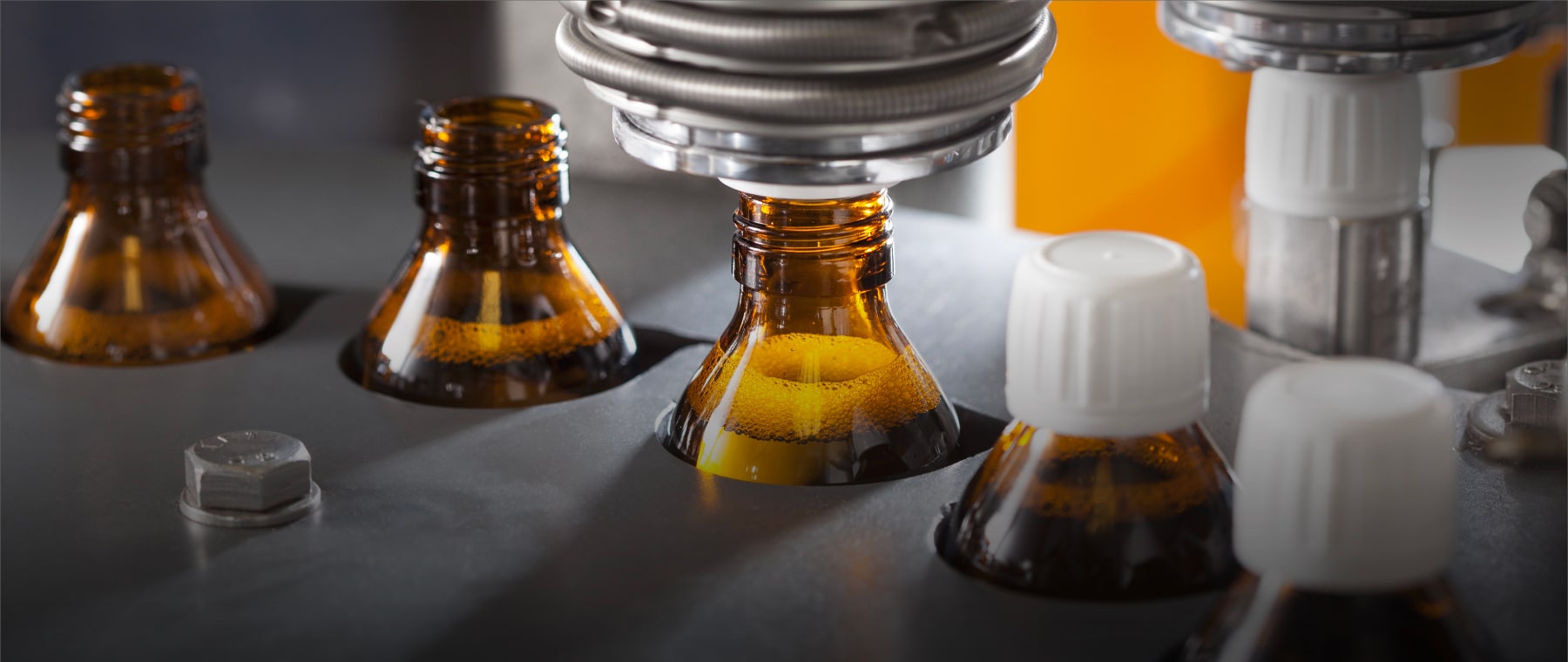
Compressed air is termed as the “Fourth Utility” for any industry. In industries like Food & Beverage or Pharmaceuticals, it is not just the compressed air, but the quality of compressed air which also plays an important role, since the multiple stages in the manufacturing process affect the quality of output.
While on one hand we see, there is an increase in operating costs, we have also to be mindful of the impact a process/ product has on the environment. Delivering quality and superiority of product, is the need of the hour!
Hence industries are challenging existing norms and looking for innovative solutions to their quality compressed air needs. From this perspective, Oil Free Compressors are emerging as a preferred solution & ideal choice.
What are Technical oil-free compressors?
In applications where compressed air directly comes in contact with the product being processed, throughout the process, manufacturers must ensure there are absolutely no impurities. In such cases Oil-free screw compressors are the preferred choice as they compress the air inside an oil-free compression chamber, which is effectively sealed to prevent lubrication oil from contaminating the compressed air.
Traditional oil-lubricated compressors or oil injected compressors are predominantly used in oil free applications with downstream filters. This arrangement delivers “Class 1” oil quality standards, which means the air will have about 0.01 mg/m3 of oil residue.
This does not meet the global compliance requirements of ISO 8573-1:2010 and ISO 8573-7. To ensure that no residual oil, airborne particulates or vapour can enter the downstream system, they must be connected with downstream air dryers and double line filters to further purify the air. This is termed as “Technical Oil Free”.
This approach appears to be cost-effective, but in reality, it results in high operation cost and higher life cycle costs.
Technical Oil Free systems also have an environmental impact
- Approximately, 2-3ppm of oil will be continuously carried into the application and into the atmosphere. This loss of oil must be continuously topped up for the entire operating life of the compressor & is a hidden cost.
- The condensate from the compressor and the downstream filters will contain traces of oil. Due to strict environmental regulations, additionally, an oil/water separator must be used, to remove the oil before letting the condensate into the atmosphere.
What are the alternatives available for us?
Owing to oil carryover and the downstream filtration, there are a lot of indirect costs associated with a Technical Oil-Free set-up: higher operating pressure, periodic cleaning of pipes & valves, disposal of oil & filters, and downtime for maintenance.
From an initial investment perspective, Technical Oil Free systems will look very lucrative. But owing to the hidden costs, indirect costs, and operating arrangements, they will also have a higher total cost of ownership. Oil Free compressor systems will easily have a 6-7% reduction in the total cost of ownership compared to Technical Oil Free systems.
Further, if not maintained periodically, there is a very high chance of oil contaminants in the compressed air system. This might result in the manufacturers scrapping or disposing of their in-process inventory or the finished goods; recalling their products; legal proceedings or safety concerns in the facility.
It might even lead to authorities revoking production permits.
It is hence strongly recommended that you reach out to compressed air experts who can evaluate your needs, understand statutory regulations, and propose a cost-effective comprehensive Compressed Air Solution for you.