Tư vấn - Srew compressorLỰA CHỌN BÌNH TÍCH ÁP PHÙ HỢP ĐỂ TỐI ƯU HIỆU SUẤT HỆ THỐNG KHÍ NÉN
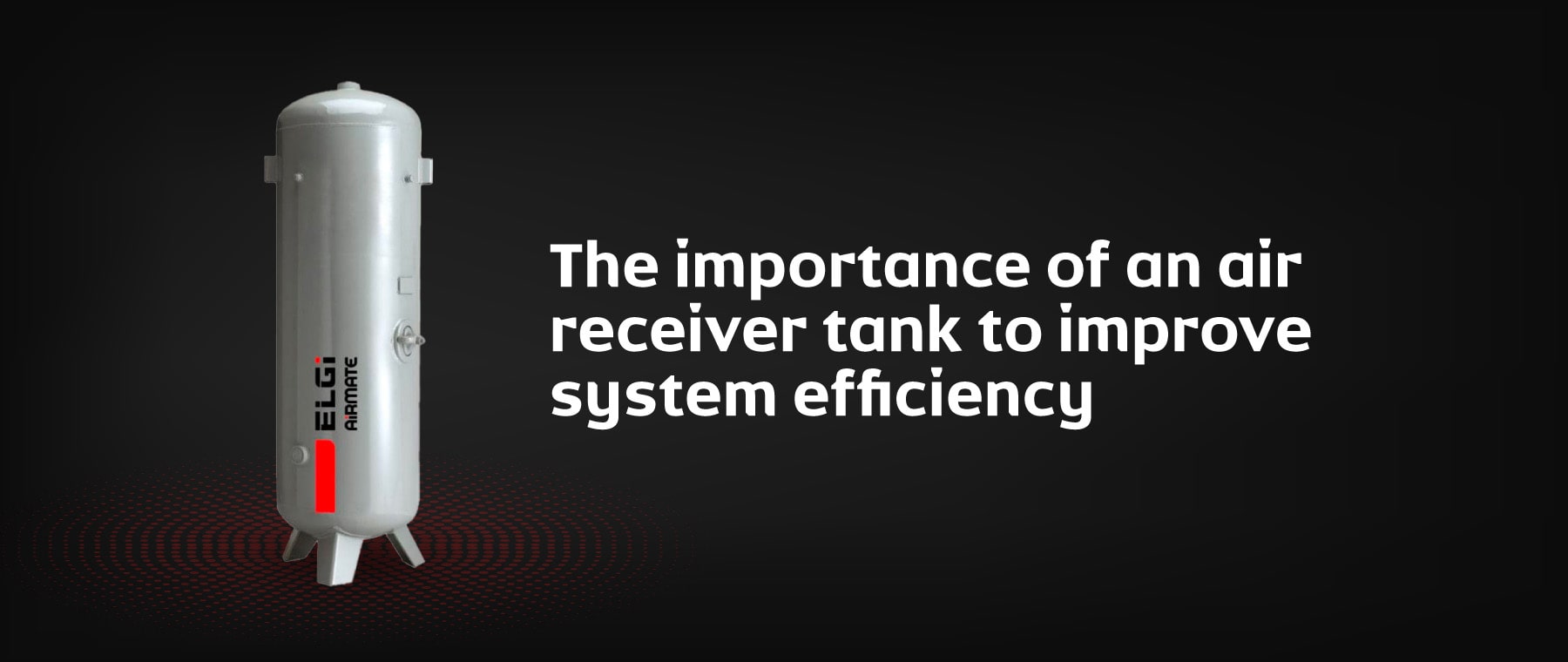
How many industries pay attention to their storage/receiver capacity design as much as it deserves? Probably only a few.
That is because, most would have gone with the rule of thumb, the usual recommendation for a typical compressed air system. But the reality is that there is more to receiver tank sizing, customized to the application than just one size fits all
Imagine a water tank at an elevated height, supplying water to residences in an area. This is analogous to an air receiver supplying to various industrial demands. Let's understand the need for an air receiver and its function in the compressed air system.
What are the benefits of Air receivers?
- Stored Energy: The primary role of an air receiver tank is to provide temporary storage for compressed air. It stores compressed air that can be used for short spikes in demand, also referred to as ‘events of sudden demand'. It also acts as a standby supply system, when tricky situations may arise at a factory including, power outage for a short period (typically switching from a grid to generator), a sudden unplanned loss of supply from a compressor (typically from breakdown), etc. Think of the importance of a battery with UPS supplying power for a computer to function without disruptions, the air receiver is that reliable battery source which enables smooth functioning of your business.
- Stabilizer: Fluctuating compressed air utilization causes uneven demand on the air compressor, resulting in rapid cycling of the air compressor controls as the air compressor turns on and off to meet moment-by-moment demand.
Each time the system turns on and off (or loads/unloads) it is called a “cycle.” It is better for the air compressor motor and other components to keep these cycles as long as possible. This is true for all upstream equipment like dryers, particle filters etc. The stabilized flow through these systems allows the equipment to function to its intended performance.
- Improves Efficiency for Air Compressors: As the air compressor cycles on and off, compressed air can be wasted. Every time a rotary screw air compressor cycles to unload, the Separator tank is blown-off from its operating pressure typically from 7 bar to near atmospheric pressure. Compressed air is released during the venting.
With cycling once every few seconds (typically under a minute) this adds up to the loss of a sizeable percentage.
- Improves Efficiency for Dryers: If used as a wet Tank (or receiver before the dryer) the receiver acts as a heat exchanger, cooling off the air and thus condensing some moisture before it reaches the dryer. The water drains out of a valve at the bottom of the tank. By removing some moisture in advance, the air receiver tank reduces the amount of work the air dryer needs to do. This is true for any dryer type from refrigerated air dryer to desiccant dryers.
- Improves efficiency for Coalescing filters: The moisture removal to some extent allows the filters to be relatively dry, in comparison to the direct handling of compressed air coming from the compressor, for the same reason as mentioned above.
TYPES OF RECEIVER TANKS
There are two types of compressed air storage: wet and dry. The tanks are the same; the difference is in where they are installed within the system.
Wet receiver tanks are located before the compressed air dryer. Some functions of the wet receiver include:
- Isolating the compressor from demand events
- Reduces/eliminates compressor cycling
- Allows the compressor to remain unloaded for a longer time
- Acts as a backup for compressor failure
Dry receiver tanks are located after the air dryers, to store compressed air that has already been dried to its desired level of the application.
- Dry compressed air is available closer to the application and is hence available in the case of a high-demand event or supply failure.
- Dry storage reduces the burden on the air dryer during high-demand events. Without a dry air receiver (but having a wet receiver only), during sudden spikes in demand, the dryer can be subject to higher volumes than the dryer is designed/rated for. This leads to lower drying efficiency and may also result in sudden pressure drops, leading to unwanted water in the air lines and the application desiring of pressure.
It is recommended that the dry receiver is larger than the wet receiver by 2 to 3 times to take care of the points mentioned above. Most applications require a combination of wet and dry storage for optimal efficiency and performance.
TYPICAL CALCULATION OF SYSTEM STORAGE
- Most systems have undersized wet air receivers
- Wet side storage can overload the air treatment equipment and hence should always be lower than the dry storage capacity.
- Avoid the use of rules of thumb (1 gallon / cfm or as a general rule of thumb air receivers should be about 25% of the FAD is inadequate in most systems) Receiver size should be Engineered to meet customer requirements.
Let's check if the rule of thumb helps the system for a compressor breakdown, followed by an auto-standby startup – which for screw compressors will be a delay of 45 seconds before it starts to generate airflow ( Typical sequence of a start is: Star to delta time delay, Stabilization, Unload run and then load run)
V = T x D x Pa
P1-P2
Where:
V = Receiver Volume
T = Time allowed for Pressure drop P1 to P2 to occur (or a disruptive event)
D = Air demand for this period
Pa = Atmospheric pressure absolute
P1 = Initial pressure in the receiver (typically the load pressure)
P2 = Lowest useful pressure required for the demand to function properly.
Assumed condition of a compressor room:
- One working compressor with one standby, with built-in automation to start immediately (within 45 sec) when compressor 1 fails. Each compressor is 500 cfm (14.2 m3/min) FAD capacity with setting of 100 psi ( 7barg) load 110 psi (7.7 barg) unload type control.
- T time available before the pressure drop affects the application is 45 sec or 0.75min
- D Air demand at the time of event/breakdown is also say 500 cfm ( 14.2 m3/min)
- Atmospheric pressure is 1 bar (14.5 psi) absolute
- P1 initial pressure in the receiver is say 100 psi, 7 bar when the compressor 1 has a breakdown.
- P2 is the lowest pressure for the application to run is 85 psi ( 5.9 bar)
Applying the formula to get the storage volume, we get
V = T x D x Pa
P1-P2
V = 0.75min x 500cfm x 14.5
(100-85)psig
Calculated Storage for 45 sec backup = 362.5 cu ft or 10.3 m3
1 gallon /cfm Rule of thumb storage = 500Gal or 66 cu ft or 1.9 m3
25% of the FAD Rule of thumb storage = 25% of 14.2 m3/min = 3.55 m3 or 125 cu ft.
If in another situation, the time to restore the standby compressor is 90 sec the storage required will be twice the above: ie
Calculated Storage for 90 sec backup = 725 cu ft or 20.6 m3
What events/ items can affect the Receiver storage sizing:
- Real events that can happen from the supply side, like compressor failures, dryer purge, power outage, are a few possibilities.
- Real events are unique to application on the demand side like, a sudden spike in demand which is more than the compressor capacity for shorter durations. These can be spotted in Air system audits.
- Useful pressure available: This is the difference between the average pressure maintained in the system to the lowest pressure it can take.
- Application and its criticality: Some processes can handle the loss of air supply for short periods, but in some cases, it will result in loss of production or complete breakdown.
- While the rule of thumb takes care of some of the intended functions like stabilization of dryer and compressor, it may fall short of others like compressor shutdown, demand spikes, etc.
The receiver tank is one of the least acknowledged champions in the compressed air system. What is also noteworthy is that, the receiver is the least expensive item that can give a return on investment in the short run!
The ease and flexibility of adding a receiver in a series at any time, makes it convenient to upgrade and improve the system, whenever necessary.
When looking to invest in any accessory for your compressed air system, it is always better to consult the experts, follow the local design codes and safety recommendations and do not deviate from the manufacturers recommended specifications.