Tư vấn - Srew compressor5 BƯỚC GIẢM CHI PHÍ NĂNG LƯỢNG CHO HỆ THỐNG KHÍ NÉN
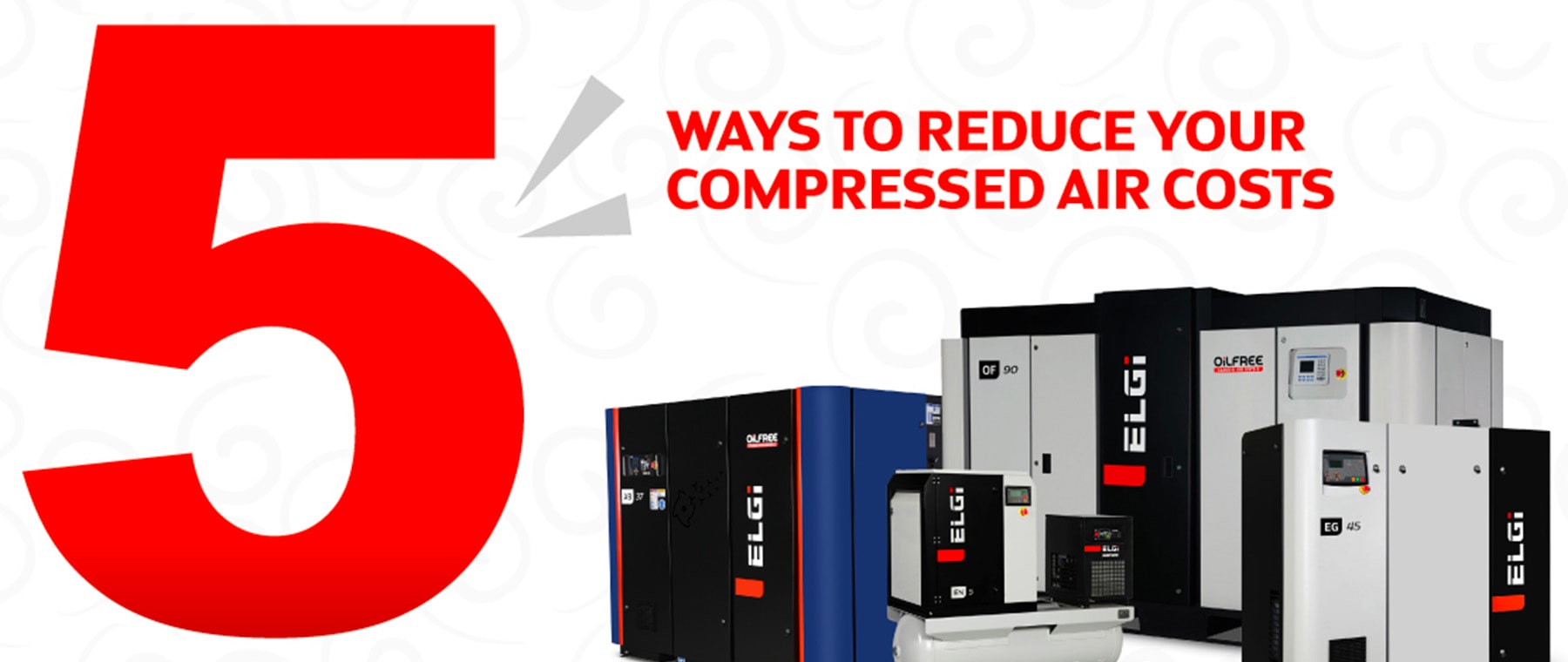
Best practices for resourceful use and efficient maintenance
Air compressors consume significant amounts of energy while fuelling industrial applications. If you take into account all the costs of running a facility, you will realise that any savings therein will lead to a positive impact on your overall cost management.
To make compressed air a more affordable utility, all you need to do is root out the inefficiencies, and maintain a sound maintenance regimen. Here are five effective ways to derive more value from your compressed air systems and reduce the related operating expenditure:
- Turn off when not in use
Many business users do not realise the amount of energy wasted when air compressors stay on idle mode.
Except in cases where a compressor must operate nonstop, like in critical application, it should be turned off during non-business hours or when the underlying application is not required. By ensuring that it is used judiciously for concerned applications, you can reduce the power consumption, leading to significant cost savings!
- Fix the leaks Another way to reduce spending on compressed air energy bills is to regularly check for and eliminate any leakage. In air compressor systems, worn or improper connections can promote air leakage and forcing the system to run in full capacity compress air. This system inefficiency can increase power consumption of the system and the user might not experience a reliable air flow.
Some leaks may be in spots that are not easy to access. In other cases, the crack may not be big enough to know if air is leaking from it. In such cases, we recommend an ultrasonic leak detector that helps you find most of those small and faint trickles before they get bigger and lead to costly issues. Get in touch with and ELGi air expert to get your system checked
- Reduce the air pressure
At many sites, users set air pressure levels to the highest limit for applications that need maximised-pressure. However, such high-pressure requirements often account for just a small part of the setup.
If you use high-pressure applications only on some days, do not hesitate to segregate them from the remaining equipment. This enables you to run the compressor at average pressure, resulting in more energy saving. The pressure should be increased only when required. To run a large facility with several compressors, you can designate a separate machine for various pressure levels.
- Examine the drains, make necessary replacements
Even though condensate drains are key features of an air compressor, their malfunctioning can cause significant harm to the system. If it does not open as intended, it begins to deteriorate the working of the air compressor.
Also, if the timer drain is jammed in an open position and does not get noticed before the next scheduled maintenance, it may cause compressed air to leak through the setup.
You can avoid such issues by adopting preventive maintenance practices and subscribing to an annual maintenance plan that will ensure efficient functioning of the system.
- Redesign piping infrastructure
The piping system design should be adequately wide for optimal airflow at the required pressure. It should allow the air to move the smallest possible length because the likelihood of pressure drop increases with long and/or complicated routing.
Shortening the distance travelled by air also reduces pressure drops by 20-40%. Such design changes in the piping infrastructure improve the efficiency of pneumatic processes and help save on operating expenditure.
In the past few years, manufacturers have customised piping for more effective use of modern compressed air systems. If your existing pipes were used with an older, smaller compressor, investment in a new arrangement would be worthwhile.