Consultant - Screw compressorUSING AIR COMPRESSORS FOR WATER WELL DRILLING
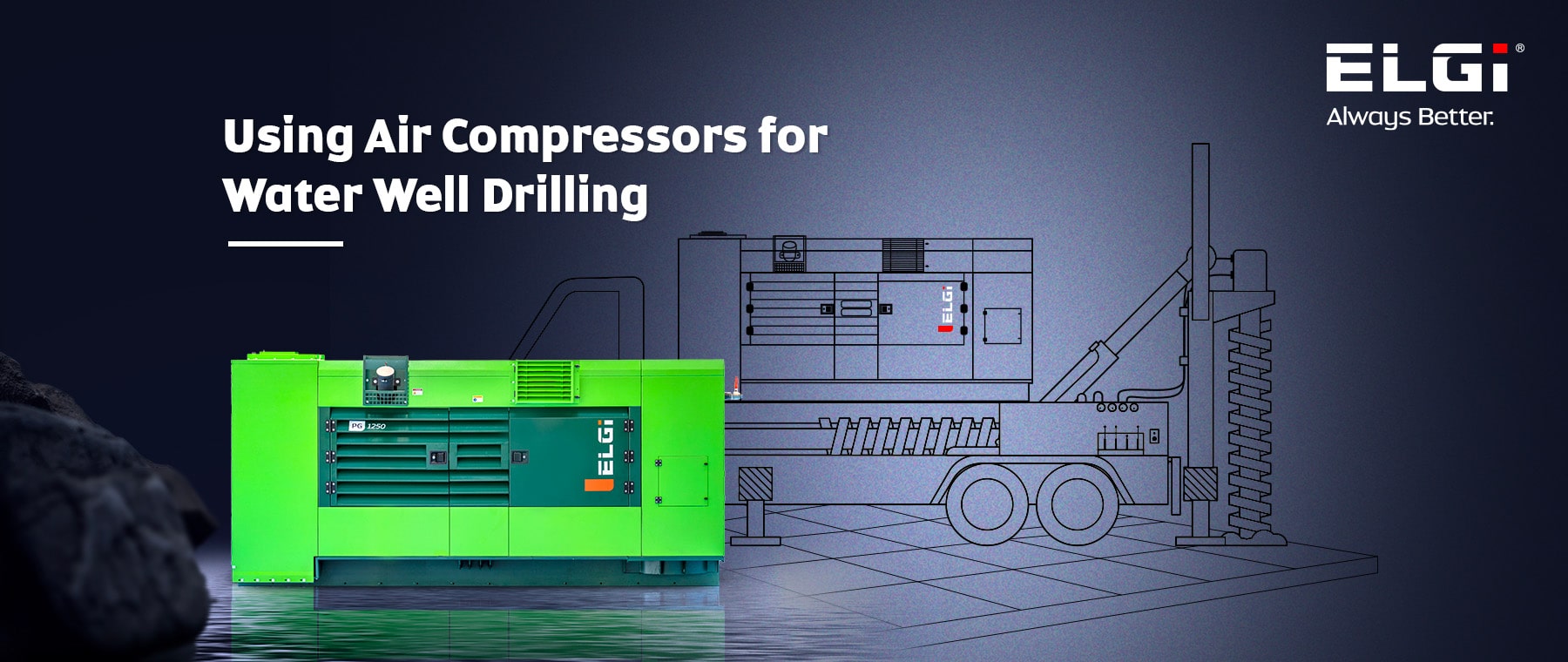
Water is a precious resource and drinking water, more precious. Humankind needs drinking water today more than ever.
In most places, water is dug out of the earth for drinking. In the olden days, wells used to be dug, but as the water table receded, depths increased, and today water wells of 4.5”-4.75”, and 6” – 6.5” are very common. Tube wells have become the order of the day to access potable water from the earth’s crust.
A brief overview of water well drilling applications
Water well drilling equipment consists of a water well rig, air compressors & accessories like drilling rods, casing pipes, and a hammer. In most cases, for deeper water well drilling, DTH drilling is adopted. DTH Drilling is an efficient way of drilling for deeper holes in medium or hard formations as hammering action is provided right on the drill bit at the bottom of the hole.
To fulfill the requirements of water well drilling applications, ELGi manufactures efficient and rugged compressors.
Here is look at the typical mounting of the equipment in water well drilling application:
Both Compressor and Rig in the same truck.
The process of drilling
Typically, a water well drill consists of the following activities:
A large hole is drilled to insert casing pipe (anywhere between 20-200 ft) using the Over Burden hammer
Which removes the top layer of the earth's crust to prevent any collapsing materials into the well.
Then, a hole of the actual size is drilled.
Today in India, the average depth ranges from 800-1200 ft depending on the water table in the zone under consideration.
Different stages of Drilling
For water well compressors, there are 2 very important aspects in any compressors.
Drilling state: In this phase, compressed air is needed at the required pressure for efficient hammer performance. The drilling state forms 75-80% of the overall drilling cycle. Compressor performance is critical in ensuring profits for the Drill rig owner.
ELGi compressors deliver the required amount of compressed air to ensure optimum drilling.
Flushing State: This phase requires the maximum flow of compressed air to remove the cuttings/debris from the hole. This state plays a critical role in determining the fuel consumption of the compressor overall, as generally, the compressor consumes more fuel if flushing is too much. Typically, flushing ranges from 10-15 % of the overall drilling cycle.
Another state is idling where the compressor delivers no air, however, it remains in that state, as the rig will undergo rod change activity.
A water well depth depends on water yield or until a customer wants to try for water. Finding a drilling point is a different topic for discussion as there are multiple ways, be it using a scientific method of using a geologist or a traditional method like using a water diviner.