Consultant - Screw compressorSMART SOLUTIONS FOR TROUBLESHOOTING YOUR COMPRESSED AIR SYSTEM
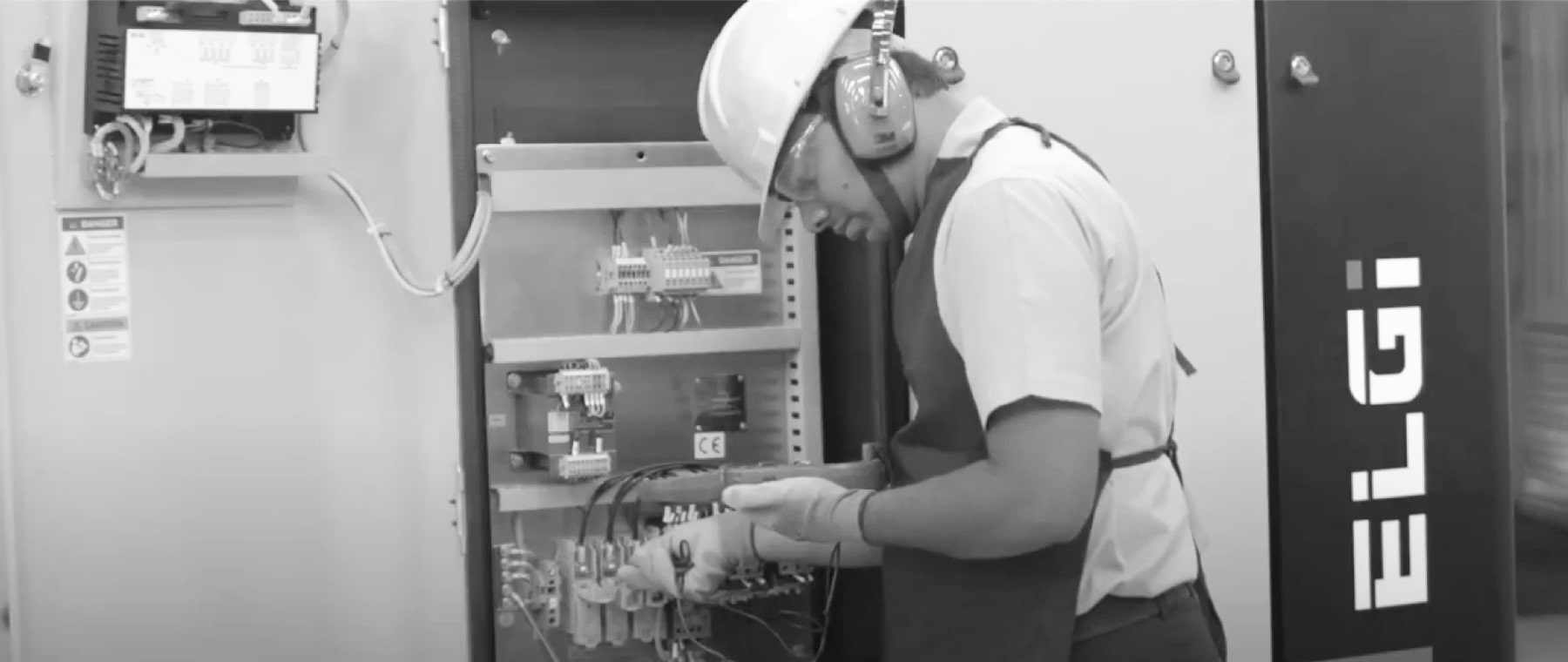
Your air compressor will show enough symptoms before breaking down. These symptoms, if not attended on time, can lead to erratic behaviour, inefficient compression processes and (or) higher power consumption, leading to eventual premature machine breakdown.
Issues such as oil carryover, air leaks, filter clogs, and inadequate lubrication are all warning signs of a gradually failing system. While all air compressor manufacturers recommend carrying out scheduled maintenance checks mandatorily, not recognizing the symptoms associated with certain issues can also lead to system failures.
So, does that mean that it is possible to identify the exact problem by simply observing the preliminary symptoms? In most cases, yes, it is.
For a customer, it is important that the functioning of a downstream equipment that relies on compressed air is not disturbed. Hence, efficient and smart troubleshooting is mandatory to save time and money. By closely observing the symptoms, we can anticipate the nature of the problem. Data must be collected, verified, and ascertained properly in order to arrive at a conclusion.
The most reported issues of an air compressor are:
- Pressure not building up or not loading
- High temperature and tripping
- Not understanding alarming and warning signals in the controller
- Tripping with high sump pressure
- Oil leakages
- Moisture condensation observed at utility point
Most of the problems can be identified through self-diagnosis of the following:
Oil levels and colour
Oil levels in the air compressor must be maintained as per the manufacturer's recommendations. Once it is below the stipulated level, the machine starts showing symptoms of a disorder. Oil levels can easily be checked by looking at the oil level indicator. The oil should only be topped up when the machine is down.
The colour of the oil is an important factor. Regularly monitor the oil and do not ignore if the colour of the oil changes to dark grey or black.
Oil storage and the container used for topping up must also be as per the manufacturer's guidelines.
Air filter
The condition of the air filter can determine the exact problem. Normally, filters are found to be dusty and require immediate attention through cleaning or replacement. Choked filters lead to increased power consumption or a dusty entry which needs to be replaced immediately.
Filters must be cleaned regularly and kept in good condition.
Motor
By checking the temperature of the motor with a temperature gun, you can determine if the machine is running normally or not. The temperature of the motor must be within the recommended limits, otherwise the chances of a failure become high.
The compressor room must be properly ventilated, as per the recommendation of the manufacturer. The customer must ensure that there is no obstruction in the airflow path.
By inspecting the hot air dissipated from the machine or by checking the air temperature by hand, the operator can easily determine if there is any problem. The operator must also look out for dust accumulations in the fins of the cooler, which can lead to hot airflow and inefficient cooling.
Coolers
The coolers must be cleaned regularly to ensure that there is no clogging or dust accumulation between its fins.
Apart from this, the health of the machine must also be checked and recorded. This will give you a detailed picture of the immediate history. Almost 90% of the problems lie in these basic diagnoses and can be carried out by anyone.
Well, prevention is better than cure. By following proactive steps stated above, customers can avoid breakdowns and downtime, improving overall productivity. If you see anything beyond what was stated above, you must connect with their compressor manufacturer immediately and rectify the faults.