Consultant - Screw compressorPOWERING GROWTH AND DEVELOPMENT IN INFRASTRUCTURE
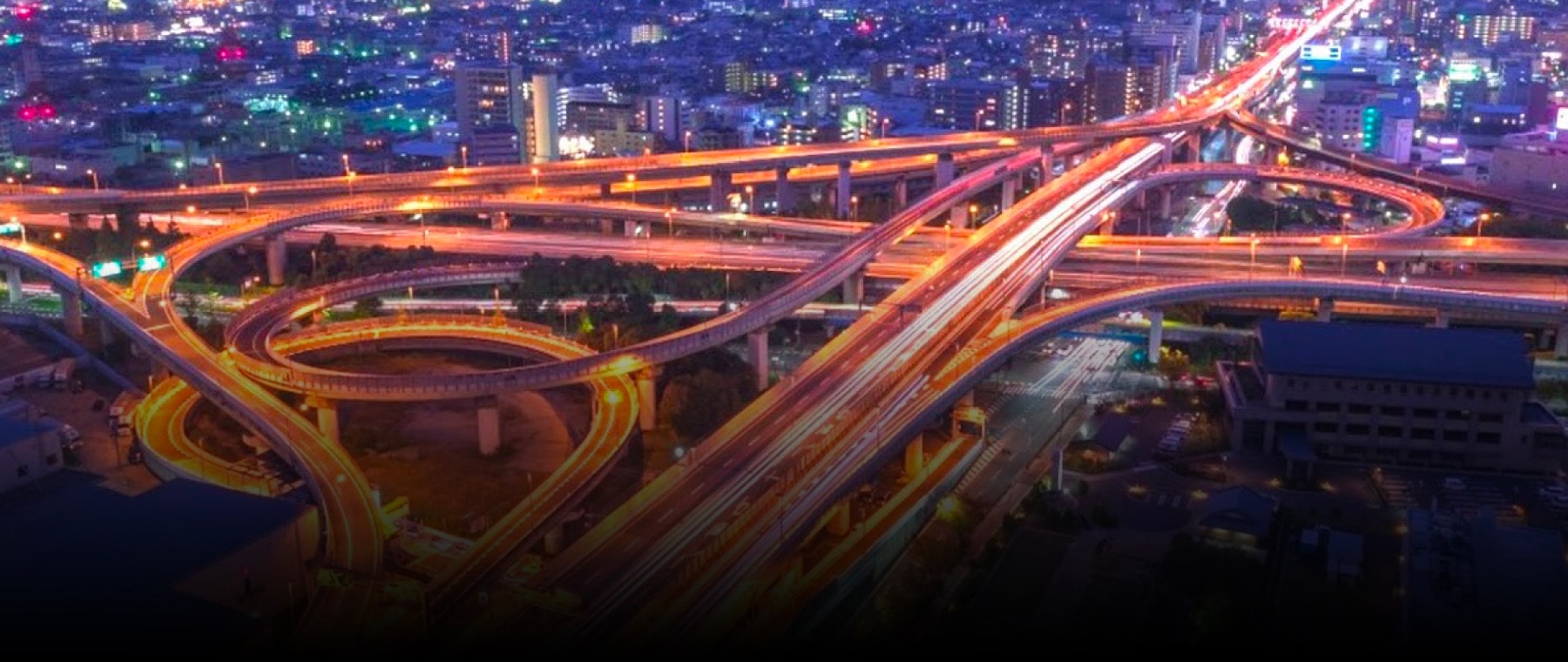
The infrastructure sector is a key driver for any economy, especially for a developing country like India. It includes power projects, dams, bridges, roads, and urban infrastructure development.
As per industry reports, India is expected to become the world’s 3rd largest construction market by 2022. Furthermore, increasing the development of the National Highways and initiatives like “Smart City Mission” provide attractive opportunities and drives the growth of this sector.
Concrete batching plants have become an essential machinery and we can’t imagine any construction site without it. In the construction industry, producing high quality concrete in the right amount and delivering it on time is a challenging task. The right quality of concrete increases the reliability of any construction and this is being achieved with concrete batching plants.
Have we ever thought what is driving the concrete batching plants to deliver the right quality concrete on time? Yes, it’s compressed air!
Let us understand the concrete batching plant briefly before going into the usage of compressed air in its operation.
What is a Concrete Batching Plant?
Concrete batching plant is an equipment in which all the aggregates such as sand, gravel, crushed stone, and slag, are batched, mixed with water, cement and other additives homogeneously to obtain a concrete of desired strength and quality.
Layout of a Concrete Batching Plant
- The aggregate bins contain sand, gravels and other aggregates
- The cement silo is a container used for the storage of bulk cement on site.
- The mixer is the heart of a batching plant, where ingredients are mixed together to form the concrete.
Operating Cycle of a Concrete Batching Plant
Charging: A cyclic process of continuously feeding all ingredients to the mixer. It ensures that the mixer is not idle and proportion of all ingredients are appropriate.
Mixing: Mixing is the complete blending of materials required for production of a homogeneous concrete.
Discharging: After mixing, the concrete mixture is evacuated from the mixing chamber to the RMC (Ready Made Concrete) truck via a discharge chute.
Compressed Air in Concrete Batching Plant
Compressed air is used in the control system typically during charging and discharging cycles to actuate pneumatic valves in the aggregate bins and the mixer. As charging, mixing & discharging are a part of a continuous operation in a concrete batching plant, the compressor must be up and running to ensure a seamless operation. Compressed air is also used to clean the silos so that the right proportion of cement and fly ash is charged ensuring desired output quality.
Criticality of Compressed Air in Concrete Batching Plant
In Aggregate Bins, valves are controlled by load sensing cells and PLC. Compressed air is required for opening these valves based on the signals from load cells for discharging aggregates to the hopper/ conveyor belt.
In the Mixer, compressed air is used for operating the pneumatic delivery valves. This aids in unloading the mixed concrete onto the ready mix concrete (RMC) truck. Concrete typically sets in from 30 to 40 minutes. If it is not delivered on time from the mixer, the concrete will set inside the mixer and leave the customer with no other option than replacing the entire mixer.
Compressed air is utilized for cleaning the silos and also for dusting the deposits in the silo walls/lining during operation. If silos are not cleaned at regular intervals, the holding capacity of silos will be reduced due to the accumulated residues resulting in decreased output quantity.
Compressed air is used as an alternative for water to clean the silos. If water is used for cleaning, the silo must be dried before loading. This process takes ample time, thereby reducing productivity.
Productivity is key for a batching plant and as compressed air plays a critical role in this, choosing the right partner for compressor is imperative.
ELGi’s range of reciprocating compressors, designed with oil bath filters as a standard part of the machine to suit batching plants, has proven to be the right product for this application’s dusty environment. The oil bath air filters are designed to offer an excellent degree of filtration, capacity for prolonged use and minimum maintenance ensuring seamless compressor performance in any external environment.