Consultant - Screw compressorOIL-FREE AIR IN MEDICINE MANUFACTURE
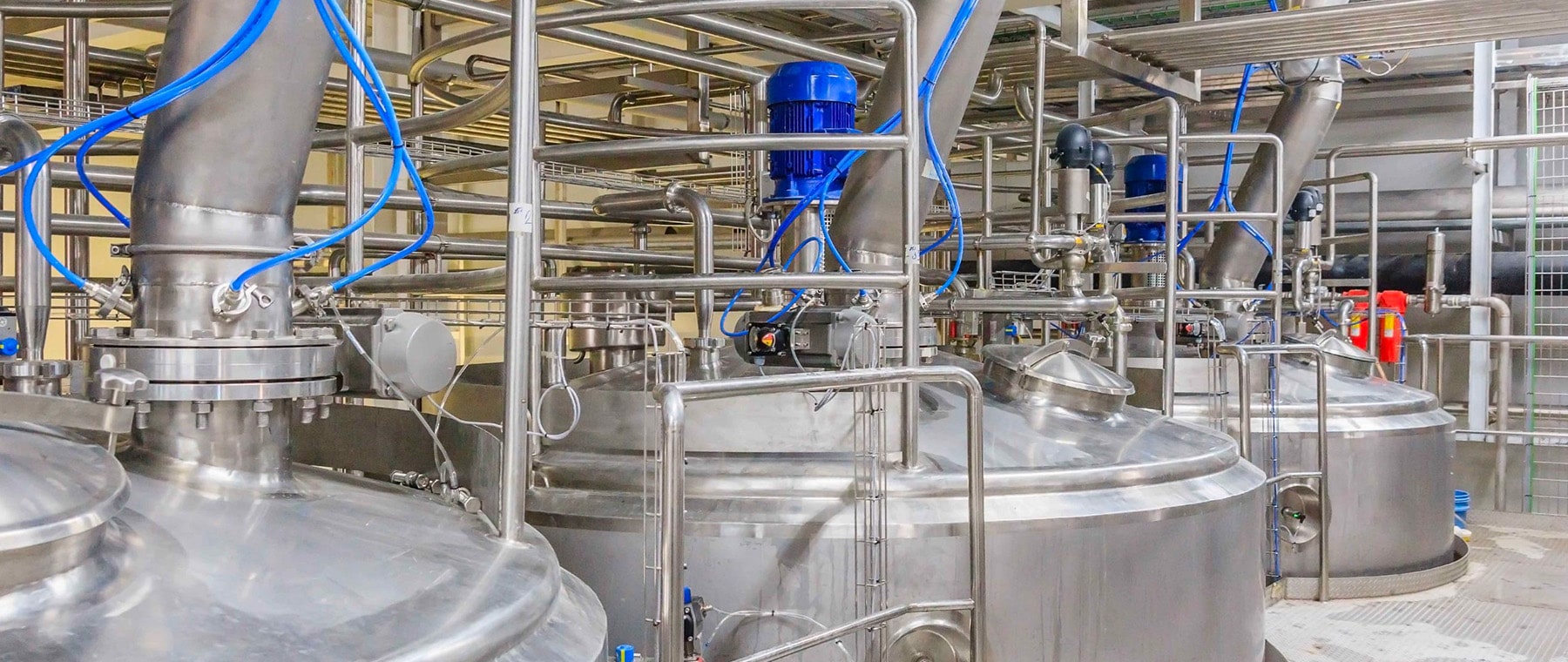
The country’s pharmaceutical industry is expected to reach $55 billion by 2020.
As we can see above, India has a great role to play in this industry with skyrocketing progress in the near future. Quality consistency will be paramount to realise this growth.
The Cost of Poor Quality
In 2010, the US Justice Department ordered GlaxoSmithKline (GSK), the British pharmaceutical giant, to pay $750 million dollars for failing to prevent contaminations in their products Kytril, Bactorban, Paxil Controlled Release (CR), and Avandamet. The Department found that Bactroban, Kytril and Avandamet could be infected with microorganisms stemming from a contaminated production facility. For Paxil CR, an antidepressant drug, missteps in the manufacturing process resulted in the pills splitting into two, offering no therapeutic effect, while others did not have the controlled release effect.
In 2012, Schering-Plough paid USD 500 million towards settlement for violation of product quality norms arising out of poor manufacturing practices for its allergy medication Claritin. In September 2013, the FDA imposed a ban on Ranbaxy's drugs that may have included human hair and oil spots in tablets. While the punitive amounts may seem large, the damage is irreversible as it is impossible to trace consumers who may have suffered from these mishaps, thus making prevention paramount. Given that such manufacture involves compressed air at every juncture, oil and contamination free air is critical to making risk free products.
Applications of Compressed Air in the Pharmaceutical Industry
Compressed air is vital to the industry and its usage can be classified into two categories; Process Air and Direct Contact. Process applications employ compressed air for a specific kinetic activity. For example, during pill production, the uncoated are churned in a large drum as part of the coating process. Compressed air often drives the drum. Similarly, it plays a large role in the conveyance process. Direct contact entails the direct contact of compressed air with the application, thus making air quality critical. For example, compressed air is used to coat tablets to ensure their structural integrity. Impurities in this air will compromise the integrity and worse, contaminate the product. It is also critical in jet milling, where nitrogen is used to reduce active ingredients. Specifically, the powder is fed into a milling chamber where compressed air or nitrogen, usually in a vortex motion, promotes particle-to-particle collisions. Particle classification is made by inertia, following reduction via impaction and abrasion.
Compressed air is used for bottle cleaning to safely remove dust and small particles from containers before filling. The system is particularly suitable for removing loose contaminants that may have accumulated during shipping or storage. Containers first enter the rinsing area and are then bathed with ionized air generated by special transvector air flow amplifiers. The static charge that attracts debris to the surface of the containers is neutralized. Rinsing heads use a blast of compressed air to clean them. A vacuum collects the loose particles which are then disposed. As a final direct application, membrane technology with nitrogen generators uses compressed air forced through a polymeric hollow fibre to selectively permeate oxygen, water vapour and other impurities out of its side walls while allowing nitrogen to flow through its centre and emerge as high purity N2 gas.
Compressed Air Standards in the Pharmaceutical Industry
The amount of allowable oil in compressed air depends on its application. ISO 8573-1 (2010) classifies the quality of air based on oil content as Class 0 to Class 4. The table below is used as a guide for selecting the compressor based on the application requirement.
The following graphic summarizes the data collected from various industries in India and neighboring countries on the quality class of oil in compressed air. It depicts that industries such as foundry and sand blasting use lower quality (class 3 or 4) air, where air quality doesn’t affect the process or the product. Industries such as food and beverage, pharmaceutical and photography demand higher quality (class 1) as the quality of air directly affects the product quality. Though Class 0 is not figured in this list, industries are moving towards using this standard to improve and safeguard their product and process quality.
Table: 1.2. Details of application requirements vs Quality class of oil
Generating Oil-Free Compressed Air
There is a growing industrial need for compressed air, free of entrained oil. For many requirements oil flooded screw compressors do the job with multi stage filtration. However, oil-free compressors are ideal owing to the hassle of pressure drops and added maintenance stemming from filter equipped lubricated compressors.
Popular compressed air systems include piston driven reciprocating compressors, screw or rotary compressors and centrifugal compressors. The rotary screw is the most widely used owing to its inherent reliability. These machines are available in a wide range of oil lubricated and oil-free versions. To understand the generation of oil-free compressed air, one must understand the role of oil in regular compressed air. Focusing on screw compressors, the heart of the compressor or the ‘airend’ works by two rotors or screws in an enclosed housing moving in opposite directions, sucking air from the atmosphere and compressing it for use in the end application.
As air travels through the airend, it is compressed to high pressure. Oil is injected into the compressed air and discharged from the compressor mixed with the air. The oil and air mixture is discharged into a gas and oil separator. After separation, the oil is cooled and filtered, then pumped back into the compressor housing, gears and bearings. In the prevailing (reciprocating and rotary) systems, oil serves as lubricant, sealant and coolant. So how do oil-free systems function without oil serving these critical functions?
In an oil-free screw compressor, an air cooler removes the heat from the compression chamber. Without oil, the rotors rotate at high speeds to get volumetric efficiencies equivalent to oil injected screw compressors. Timing gears synchronize rotation to ensure no contact. A separate lubrication system lubricates the timing gears. And finally, an efficient sealing system prevents the entry of lubricating oil into the compression chamber.
Typical assembly cut view of ELGi Oil-free airend used in oil-free compressor
Quality By Design (QbD)
Pioneered by Joseph M. Juran, Quality by Design is an approach that helps prevent the occurrence of quality lapses in high risk industries such as drug manufacture. Design for quality and innovation is one of the three universal processes of the Juran Trilogy. The focus of this concept is on quality that should be built into a product with an understanding of the product and process by which it is developed and manufactured along with a knowledge of the risks involved in manufacturing and how best to mitigate them.
Applying this to oil-free air in the pharmaceutical industry, QbD principles would dictate design measures to prevent contamination in the delivered air. As an example, ELGi’s oil-free rotors employ a two-layer non-metallic coating and coating process to preserve the rotors. This coating comprises of PTFE + PFA (Poly Tetra Fluoro Ethylene + Per Fluoro Alkoxy), with PTFE on the first layer and PFA on the top.
PFA has layering and formation properties which ensure homogeneous coating and avoid the formation of pin holes. This enhances the coating reliability and provides highly efficient corrosion protection. In addition the coating serves as a dry lubricant. The coating’s food and medical grade certification ensures its safety for pharmaceutical applications. Though there is no oil injected into the compression chamber, the timing gears and bearings need lubrication through a separate system. This oil is prevented from entering the compression chamber with ELGi’s efficient internally designed sealing system comprising of floating carbon seal and viscose on each rotor. These are non-contact seals and their reliability is significantly higher than any other, hence ensuring continuous clean air supply.
The Future of Oil-Free Air
Rough estimates indicate that oil flooded screw compressors have expelled nearly 10 million liters of oil into the atmosphere over the past ten years. The amount is humbling given the growing stresses placed on the planet. Thus it is clear that oil-free air is set to grow in relevance not just for the pharmaceutical industry but for all applications. The current oil-free technology struggles to compete with traditional oil flooded machines. Given the higher rotor speeds, rotor complexity and increased parts for cooling, they’re typically more expensive and less efficient, causing crippling barriers for their adoption. To overcome this, companies such as ELGi are taking a two pronged approach. The first is a philosophical shift to no longer look at oil flooded and oil-free as distinct segments. Secondly, to simplify current oil-free technology to reduce cost and improve efficiency, ELGi is working on water injection processes.
To reduce risks, ELGi has started delivering compressors with data transmitters. The sensors pick up variations in volume, pressure, temperature, moisture, etc., and feed this data back to the service and quality team to proactively address issues in the line. This technology will likely be extended to detecting air contamination, which can allow ELGi to partner closely with its customers in ensuring quality.
Compressed air will be relevant to the pharmaceutical industry for the foreseeable future. Oil-free compressed air will become more prevalent supported by design initiatives to improve cost and efficiency. Data will serve as a key enabler but more importantly, the suppliers and manufacturers need to work as a team to eliminate quality concerns.