Consultant - Screw compressorIT’S SHOE BUSINESS
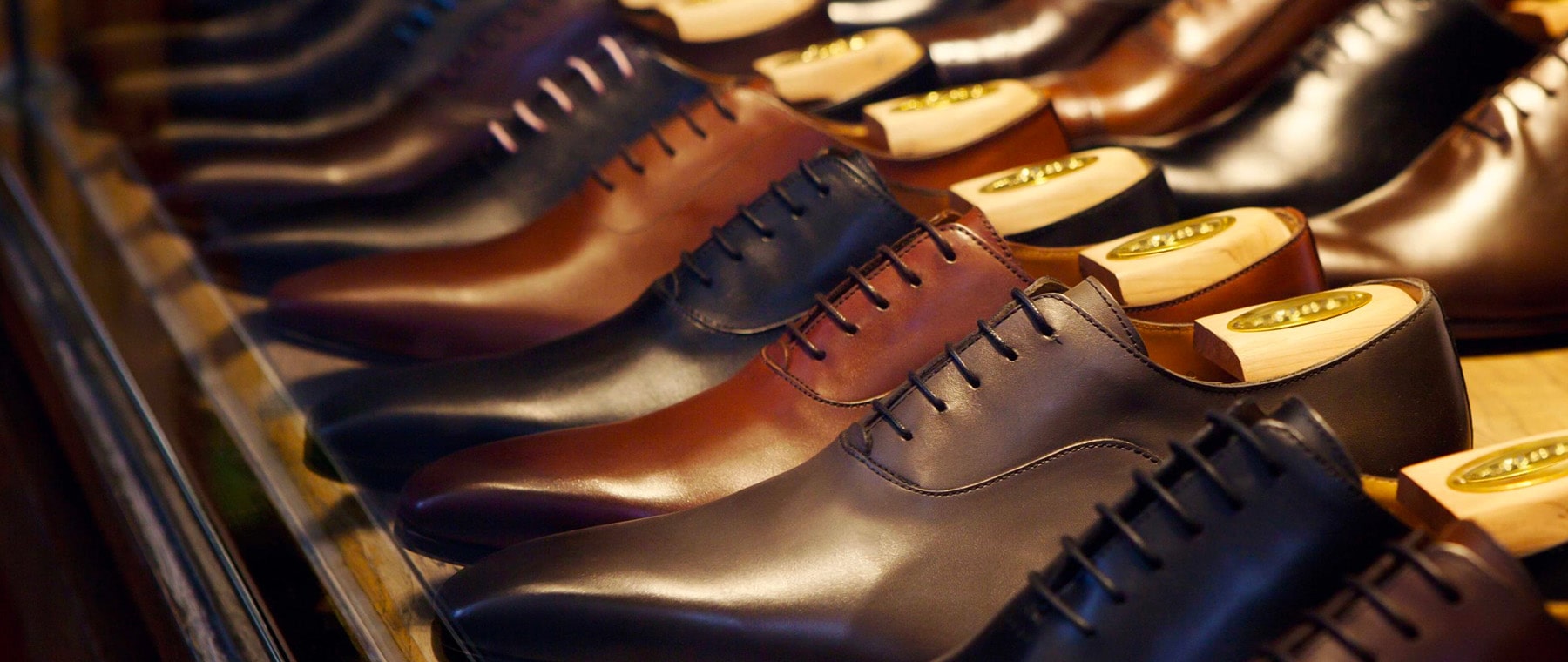
The air is heavy with the unmistakable scent of leather. Both man and machine move in tandem with a precision that is hard to fathom. In less than a minute, 24 conveyor belts churn out the Summer Spring 2017 collection of impeccably crafted Red Tape shoes. We’re in “Leather City of India”, Kanpur at the production plant and tannery of Mirza International Limited. One thing is immediately obvious –– time is of the essence.
The shoe business is serious business. With fashion trends changing at the drop of a hat, one cannot afford to blink and miss. From the runways of Milan to street style in Durban, international brands must keep their designs relevant across the globe. Mirza International Limited is India’s leading manufacturer and exporter of leather footwear and finished leather. Red Tape is their flagship brand of premium footwear with a strong presence in over 30 countries. At this level, the exigencies of the business are incessant.
“UK, USA, Europe, New Zealand, South Africa, Middle East….retailers everywhere keep changing collections to match global trends and demand new designs with a quick turnaround time. Enter the market too late and you could end up with dead stock,” says Plant Manager, Mr. Ambarish Srivastava.
Mr. Ambarish Srivastava has been working with Mirza International Limited since 1994. As Plant Manager of their Kanpur unit, he helps keep a watertight system in place; ensuring maximum efficiency at every step of production from ‘raw to retail’. With more than two decades of experience in the leather industry, Mr. Ambarish knows the nitty gritties of the business. “Handling leather is an art in itself. The textures, the surface finishes, the natural imperfections are all hallmarks of genuine leather. We strive to preserve this quality during the process of treating the leather,” Mr. Ambarish elucidates.
Strips of exotic leathers are artfully cut to in various shapes to form the top part of the shoe, called the ‘upper’.
Compressed air finds application in the finishing stages of leather at the company’s state-of-the-art tannery. A spray of compressed air is used to sanitize the leather surface by removing dust particles and other impurities. The dew point of compressed air is crucial here. “Any moisture in the compressed air can be detrimental to the leather. It could result in poor color or a patchiness that is undesirable. We have very strict specifications for the quality of air that comes in contact with our leather,” adds Mr. Ambarish.
Moving on to the production plant where the actual shoe is put together, the clockwork-like assembly line is composed of state-of-the-art machines and backed by expert leather craftsmen. The ideal production capacity of the plant is 7 million pairs of shoes per annum and the plant manages to reach 70-80% of its capacity –– at a whopping number of 6 million pairs a year, this is no mean feat. 90% of the tools and machines are controlled pneumatically. Consequently, the supply of compressed air is critical to the functioning of the plant.
Sole stitching done by the hands of seasoned leather craftsmen.
“Our conveyors deliver over 2100 pairs of finished leather shoes per hour. If air compressors break down, production would stop immediately. Today, Red Tape shoes are available in over 300 prime outlets and 1200 shop windows all over the world, in addition to prominent e-commerce websites. The demand is high and we simply cannot afford to have any hold-ups,” Mr Ambarish points out.
Established in 1979, Mirza International Limited (formerly known as Mirza Tanners) has trusted ELGi for its compressed air supply. The company sources the machines from exclusive ELGi dealers in Kanpur, Auto Service Equipment. Mr Ambarish elaborates: “The plant utilizes 35 compressed air systems. We are extremely happy with the service. In case of downtime, air supply is restored within 90 minutes which is remarkable. It ensures smooth running of the plant and maximum output which is very important for us. In my 23 years of working here, we have never felt the need to hire in-house technical staff to inspect our compressed air systems. The ELGi team is always there to help us out.”
In 2016, after performing a thorough analysis of the ELGi compressed air systems installed, the technical team at ELGi recommended a brand new facelift for Mirza International Limited. ELGi set up their latest “Global Series” air compressors (EG75) at the plant. “After the installation, we have charted about 75,000-80000 INR of energy savings a month. That’s 15-20% of our total energy costs…a significant achievement,” says Mr. Ambarish.
Seat lasting is a crucial step in shoe making that gives the ‘upper’ its shape.
Since the launch of the brand in 1996, Red Tape has garnered a premium brand status, both in Indian and international markets, especially in Europe. The brand boasts of a 25% market share in the middle-segment category for men’s shoes in the UK. With fashion experts, footwear and leather technologists as part of the team, the brand is known worldwide for its lasting quality, and compelling designs.
On being quizzed about the number of years ELGi has been in business with Mirza International Limited, Mr. Ambarish smiles and signs off, “Many, many years. ELGi was the first compressor installed at the tannery right at its inception around the 1980s. There has been no looking back ever since.” He hurries back to work as the air resonates with a low hum of the machines relaying one spectacular shoe after the other. The clockwork of the plant keeps ticking. Time, after all, is of the essence.