Consultant - Screw compressorINTRODUCING ELGI'S AF SERIES DOWNSTREAM FILTERS.
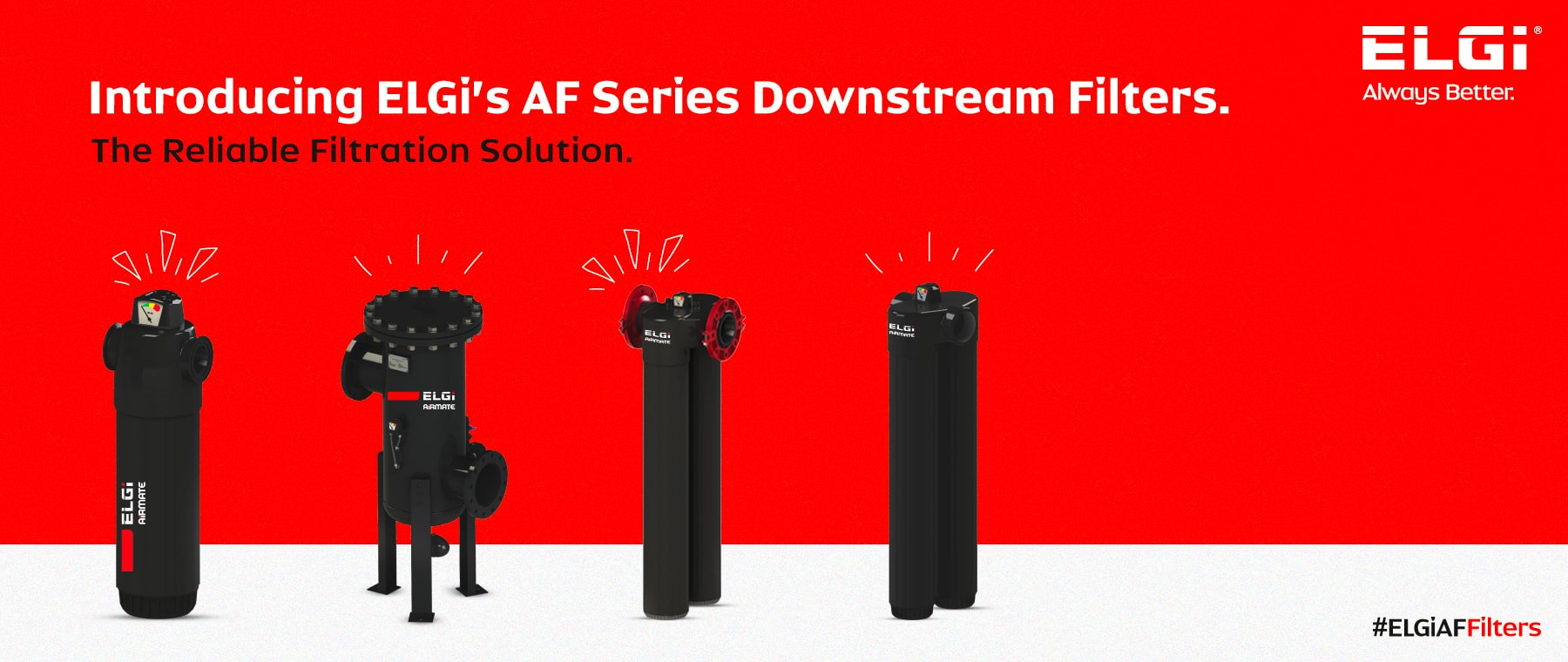
Why ELGi Airmate Filters?
Here are the three key values that the customers gain with the ELGi's AF Series Filters.
- Best-in-class performance: These filters are third-party tested for performance of residual oil as per the class stated and handle capacity they are rated for with high efficiency (99.99%).
- Best-in-class energy efficiency: The AF series filters have the lowest pressure drop in their class and significantly save energy wastage. The lowest pressure drop of 0.35 bar (combination of wet saturated pre-filter, fine-filter, and dry carbon filter) at rated capacity with next-gen elements is about 30% lower than average competition.
- Best-in-class ten years warranty for housing: The common problem with most housing is corrosion. While this corrosion doesn't affect the filter's performance itself, it adds particles of its corroded body (Al or Fe) to the air, thus making it unfit for sensitive applications. With this warranty, customers can have a reliable, pure operation for the entire life of the filter.
The above value proposition is backed by tests (as per ISO 12500 standard), validation data, and third-party certification. The maintenance of these filters for changing the elements is made reliable and simple. The differential pressure gauge gives the actual condition of the element, i.e., three coloured indicator helps in easy identification of filter element life and planning the maintenance activity. They also come with an element-time strip indicator that helps alert the user for on-time replacement of elements, thus never missing the reliability and quality of air needed by any user. You can contact ELGi application engineers or the nearest sales representative to select the right product for your application.
Application of Downstream Filters
How to remove contaminants from your compressed air system?
The atmospheric air comprises of moisture, particle contaminants, microorganisms, and gases. When this air gets compressed, the concentration of such particles increases by 6-10 times. However, when an air compressor compresses this atmospheric air, other contaminants like oil and metal traces get added during the compression process. This is why it is important to remove these contaminants from the compressed air before using them for any application.
These contaminants can be categorized into:
- Particles
- Water (Liquid, vapour, and aerosol)
- Oil (Liquid, vapour, and aerosol)
- Microorganisms
- Other gases
According to the International Standard, ISO 8573-1:2010, compressed air contaminants like particles, water, and oil are segregated as per purity classes. In this standard, microorganisms and other gases are not included. As a result, the air purity is indicated as [P, W, O] and is ordered as per the number of particles, water, and oil.
Based on the application requirement, contaminants are to be removed from the compressed air using suitable downstream equipment. For instance, particle, water, and oil contaminants can be removed from the compressed air using downstream filters.
Bulk moisture separators are recommended for removing the water from the compressed air. It is mandatory to have a proper automatic drain along with the moisture separator, as they are mostly used after the cooler. The optimal removal of condensate will ensure that no bulk water carry over to the downstream equipment. It is recommended to use a level sensing zero loss drain along with a moisture separator to get this done with minimum loss of air.
Downstream filters are available in various configurations/types. These can be categorized as per the residual oil and particle after filtration and are as follows:
- The Coalescing filters are recommended to remove the wet particles and aerosols (water and oil) from the compressed air. Different types of coalescing filters are available based on residual oil and particle content at the filter outlet after filtration. Coalescing filters are classified into pre filters and fine filters.
- With the Pre-filter, class 3 or 2 purity of particles and oil can be achieved, i.e., ISO 8573-1:2010 [2:-:2]
- The recommended sequence of installation is the bulk moisture separator followed by pre-filter
- With the fine-filter, class 2 or 1 purity of particles and oil can be achieved, i.e., ISO 8573-1:2010 [1:-:1]
- The recommended sequence of installation is bulk moisture separator, pre-filter, dryer followed by a fine filter
- The particulate filters are specialized to remove the dry particle and microorganisms from compressed air. This filter is mostly used after a desiccant dryer to ensure that the desiccant particles are not carried to the compressed air line.
- The class of purity of particles made possible with this filter is 3,4,5&6, i.e. ISO 8573-1:2010 [3:-: - ]
- The recommended installation sequence is the bulk moisture separator, pre-filter, desiccant dryer, followed by the particulate filter.
- The Carbon filters are recommended to remove the oil vapor and other gases present in the compressed air that are not removed by the coalescing filters.
- The class of purity achievable with carbon filter is "1", i.e., ISO 8573-1:2010 [-:-:1]
- The recommended preceding with carbon filter would be pre-filter, dryer, fine-filter, followed by carbon filter
Important factors to consider for having the right selection of filters to ensure optimal performance
- The filter capacity is based on the operating pressure of 7 bar/100 psi (nominal condition). In case the operating pressure is different, it is important to use the correction factor and select the filter model accordingly.
- The correct sequence of installing filters must be followed so that the performance is optimal. As a thumb rule, the level of filtration should be in sequence, ranging from 20 ppm to 5 microns or from 10 microns to 1 micron to 0.01 micron. Carbon filters should always follow after the 0.01 micron filter. Absence of this sequence will reduce the life of the filters.
Please note that the lowest pressure drop across filters happens when the filter elements are dry. If the filter element gets wet, delta P will increase. This is another reason why we should follow the above sequence.
It is recommended to have a proper drain along with the pre-filter since the pre-filter is mostly used before the dryer. The regular removal of condensate will ensure that no moisture carries over to the downstream equipment.
The replacement of the filter element at the recommended service interval is important. The filters have an indicator of saturation level, and it is recommended to replace the filter element in case of indication. Saturated filter elements will not give the required class of purity. This will have a higher pressure drop, creating an extra load on the compressor. As a thumb rule, 0.14bar/2 psi pressure drop will have 1% additional load on the compressor. Carbon filters function on the adsorption method and need to be replaced on a timely basis.