Consultant - Screw compressorIDENTIFY THE REAL LIFE CYCLE COSTS OF YOUR AIR COMPRESSOR
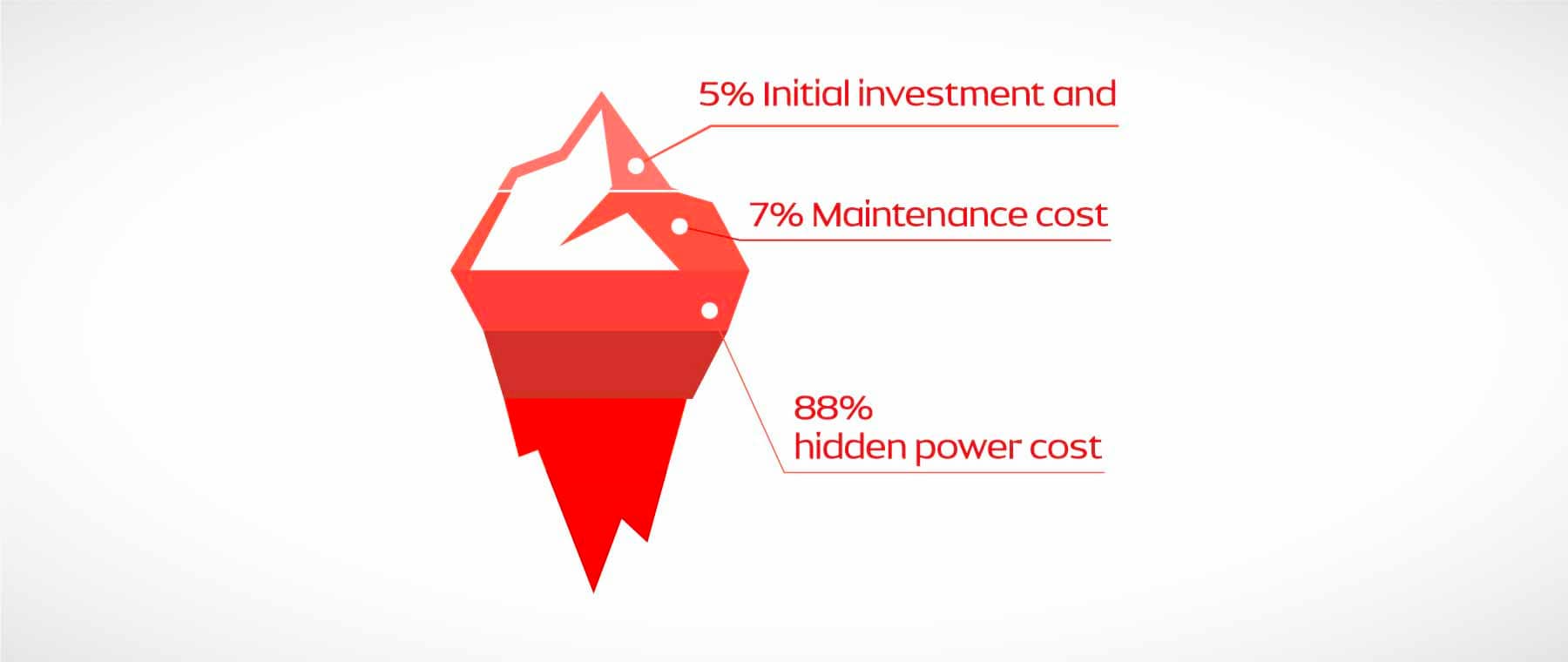
“Cost is king…” is a popular saying among the business circles and there could not be a better time than now to understand its implications.
The current pandemic situation has reiterated the significance of cost. Decisions regarding capital expenditure are being critically reviewed, as every organization is looking at ways for better cash management. In such scenarios, where expenditure is essential, there, every penny saved is equal to cash earned.
Air compressors are among the most important equipment used for varied applications across industries. Air compressors come in different types, sizes and makes. From its utility perspective, air compressors are machines which consume power. Every kW of power consumed is money spent / cost incurred.
Apart from the electricity cost, there is also the cost associated with maintenance and upkeep of the equipment. These are recurring costs incurred through the life of the compressors, to keep them in operation. Hence it is important to understand the different costs associated with air compressors and their contribution towards expenditure.
The overall cost incurred in procuring, maintaining and operating the equipment is often called as the “Total Cost of Ownership (TCO)” or “Life Cycle Cost (LCC)”. There are three main elements of cost used in calculating the life cycle cost, they are (1) Power /electricity cost (2) Overall maintenance cost, and (3) Initial investment
(1) Power Cost:
The electricity charges to operate the compressors are termed as power cost. The duty cycle of the compressor (i.e. full load or partial load) is an important factor while computing the power cost. Since air compressors are capital equipment, they should be operated on its full load capacity to reap its full benefits. Partial load cycle means the equipment will blow off air during the unload phase, which is (economically) undesirable. Power cost is always calculated as cost of power when the compressors run in loaded and unloaded condition. This is by far the most significant component of compressor life cycle cost.
(2) Maintenance Cost:
The cost associated with keeping the compressor in good working condition is called maintenance cost. The key costs included are the cost of consumables like air filter, oil filter, oil, separator elements, refrigerants, desiccants, and valves which must be replaced at regular intervals as recommended by the manufacturer. The cost of regular spares, kit parts and critical parts should also be included. Labour is the additional cost incurred along with compressor maintenance when hiring a professional. In most of the cases, cost of the annual maintenance contract (AMC) would also be involved.
(3) Initial investment:
The cost of purchasing the air compressors, its accessories and associated installation costs are referred to as the initial investment. During each purchase & installation, decision makers will evaluate all possible options to ensure optimum investment in procurement.
Hence life cycle cost is the sum of the three factors mentioned above. This can mathematically be expressed as:
Life Cycle Cost = Power Cost+ Maintenance Cost + Initial Investment
The above figure illustrates the contribution of the three elements in calculating the overall life cycle cost of the compressor. As can be observed, the power cost plays a vital role.
It is essential to understand the maintenance costs and the power consumption of the compressor during the procurement phase itself. The reason is that equipment costing less might involve frequent maintenance and consume higher power.