Consultant - Screw compressorCOMPRESSED AIR PIPING SYSTEMS
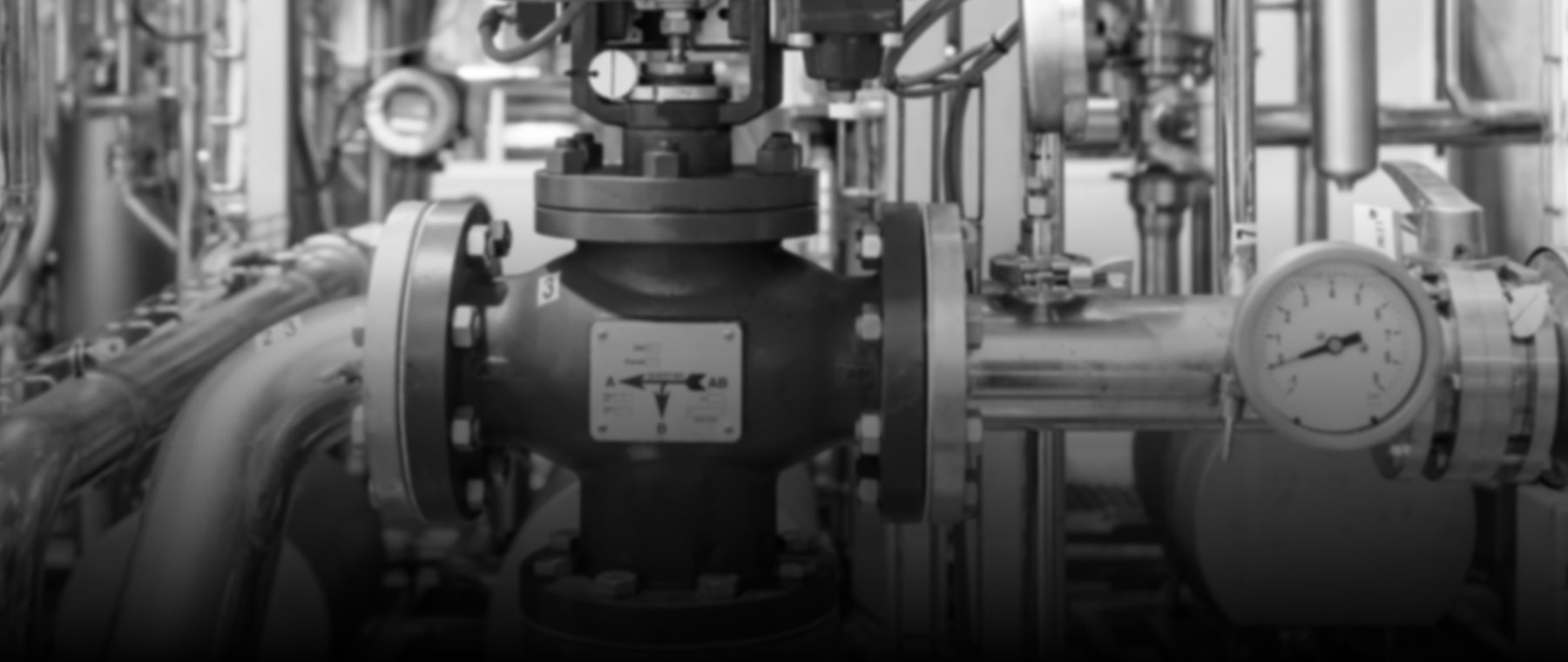
Impact of faulty component selection
A faulty layout, design, and selection of pipe material will cut down profits by: - Increasing the energy consumed in your air compressor - Resulting in the failure of the equipment - Reducing production efficiency - Increasing maintenance costs
What should be the key focus points in a pipe layout and design?
Fixing leaks is the first thought that pops up in your head! But there is a lot more to your compressed air system. Here is a list of additional components to be considered for efficient transmission and better quality of compressed air:
- Air-receiver - It is the primary storage for compressed air to balance the output pressure and application need. The selection of an air-receiver is crucial to meet the demands of the plant, along with the effective operation of the compressor (load / unload).
- Size - Appropriate selection of the size of the pipe, based on CFM of the compressor, will minimize the pressure drop, thereby reducing energy consumption. The larger the size of the pipe, the lower is the pressure drop.
- Bends - A straight path for the air is the most efficient. When it comes to bends, a large radius bend is the most preferred. It reduces turbulence, thereby reducing the pressure drop. Note: Avoid short bends as much as possible.
- Drop-line - Drop line tapping should always be from the top of the main header line, curved down to the application point.
- Moisture drain points - Moisture drain points at the right place with Auto drain valve, will drain the water from the system.
- Closed-loop design - It is the most efficient piping layout. There is no beginning or end for the header line, just a continuous loop.
Planning for the long-term is always crucial for the continuity of your business. Hence, when you follow structure, recommendations and timely upgrades in your expansion plans, you are at a better place, avoiding any expensive modifications.
What compressor piping systems are available for businesses?
- Aluminum pipes - The latest technology, Aluminum, is light-weight, making it easy to handle, and is highly recommended for clean air applications. It is non-corrosive and remains leak-free.
- Galvanized pipes - Galvanized steel pipes are widely used in compressed air systems. However, over time, the galvanizing coating flakes off and affects the application equipment in the line.
- PVC pipes - PVC pipes are commonly used in compressed air systems, mostly because they are readily available, inexpensive, and easy to install.
Air accessories for the effective operation of your plant
To complete your compressed air system, you will need to analyse the requirements of your equipment, and accordingly choose the accessories which deliver the best quality and quantity of compressed air for the effective operation of your plant.
- Line filters - Compressed air will contain dirt, moisture, scales, and other impurities. The purity of air plays a significant role in the sterility of processes, especially in sensitive industries including food, beverage, and pharma. Installation of filters will ensure that your application remains oil and dir free.
It is also necessary to replace the cartridges at recommended intervals to maintain air quality.
- Dryer - The presence of moisture in the compressed air system, will damage pipelines, tools, and equipment that utilise compressed air. You must select a dryer for your system depending on the moisture tolerance level of the equipment. Dryers are effective in removing moisture and delivering moisture free air for further processes within the system.
- Drain valves - Zero loss drain valves are highly efficient and reliable. The condensate level is sensed and the moisture/condensate is drained completely, with no loss of air.
- Condensate treatment - A mix of oil-water (condensate) is bound to be present in the system. It is always recommended to treat this mixture before releasing it to the sewage-disposal phase. A Condensate treatment unit (Oil-water separator) will help you carry out this activity to dispose of the condensate.
- Measure the effectiveness of your compressed air system periodically- This can be done by simple visual checks for leakage, monitoring the condition of filters for a pressure drop, analyzing the application pressure, and finally, adjusting and adapting to the changing needs.
Air audit data is the most reliable source of information for reducing the operation cost. Depending on the demand pattern, you can arrive at a solution which will decide on the use of VFD or sizing of your compressor.