Consultant - Screw compressorCOMPRESSED AIR ISN'T FREE
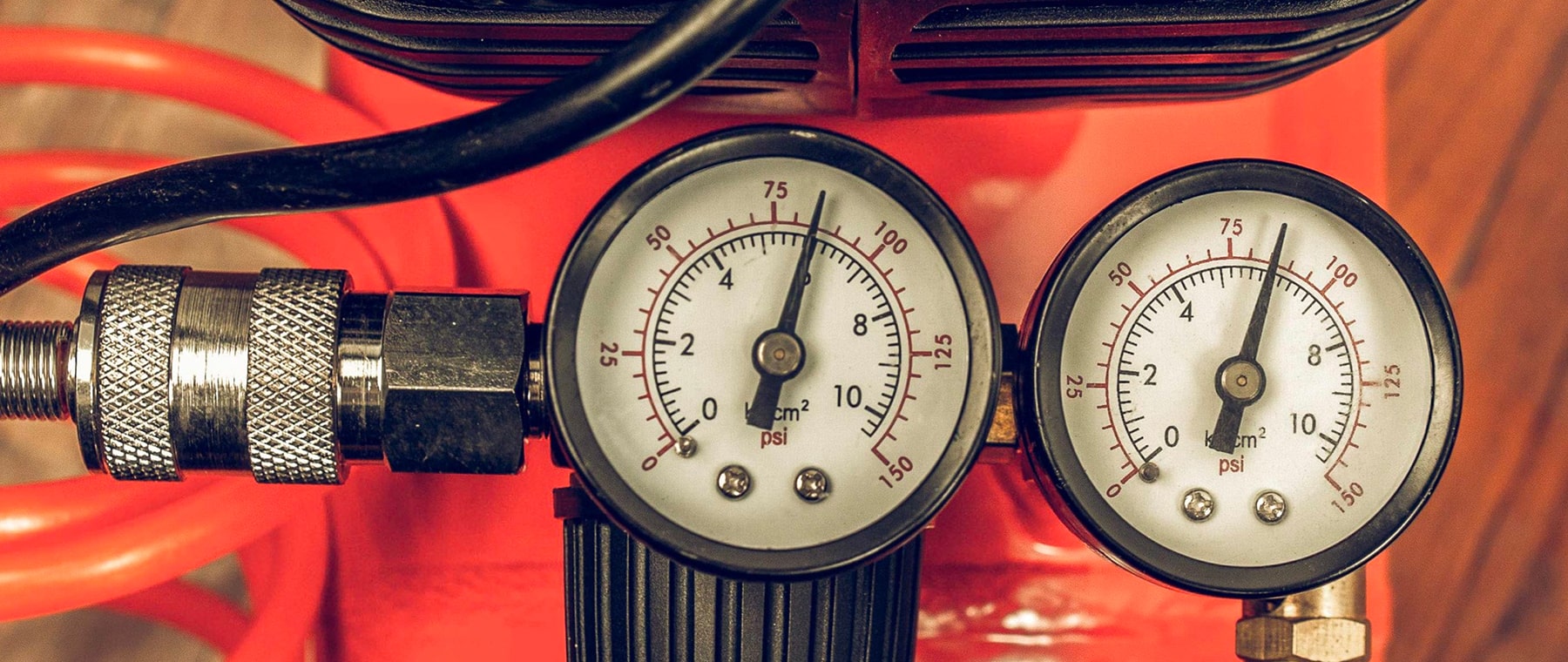
While there is significant awareness in industries about energy efficiency and carbon reduction, we tend to overlook a massive opportunity right under our proverbial noses.
Compressed air can certainly save your pocket a fair bit of change but inefficiency and negligence can make it a saving liability. Alarming news, considering market studies indicate that in various industries compressed air accounts for 10 to 30 percent of the entire energy consumed.
How much is wasted energy costing me?
A 100 hp air compressor can incur a cost of $40000 annually in energy alone. And up to 50% of that may be wasted. On average, the share of electricity in the operating cost of a compressed air system amounts to 76 percent.
Leaks in the compressed air system are a significant part of the problem but a greater issue is a mismatch in the demand and supply within the system. Therefore, to optimize a compressed air system one should start with optimizing the demand and the supply. Here's how to do it -
Six Steps To Optimise Your Compressed Air System -
Demand
- Establish the correct air requirements (flow and pressure) of each point-of-use.
Distribution
- Establish the leakage points in your system and manage them.
- Analyse the system capacity and optimise it.
- Analyse the fluctuations in demand and manage them efficiently.
- Track the pressure profiles across the plant for supply-demand mismatches and minimise the pressure drops.
Supply
Evaluate the health of each compressor and the support systems. Optimise the controls to match the system dynamics.
Demand
Step 1 on optimizing demand is to plug up the leaks! These are typically located at the point-of-use connections, filter-regulator lubrication units, solenoid banks and hoses. Nothing that regular maintenance can't fix.
Maintenance is also important to prevent pressure drops. The nominal pressure drop in the system from the compressor to the farthest end of the facility should be less than 10 psig. Common culprits of this are - plugged filters, old dryers, inadequately sized pipes and excessive or sharp bends in pipes.
Using appropriate pressure settings at the end users is essential, because an unwarranted high pressure results in an increased use of air, creating an artificial demand on the compressor.
Solenoid valves must be installed to shut off air. These valves can be interlocked with machine operations so that when a machine or line shuts down, the air flow to that machine or line is shut off, thus eliminating leaks.
Supply
The supply side refers to how the compressed air is generated.
The discharge pressure set point must be reduced as much as possible.
There is a 1% reduction in power consumption for every 2 psig reduction at the compressor. This also reduces the leakage losses.
Efficient part-load compressors and controls need to be installed.
If a facility has a constant requirement then one compressor is efficient but for fluctuating loads a combination of compressors is more prudent.
A large storage capacity is desirable.
For load/unload-type compressors, the storage capacity should optimally be in the range of 3 to 10 gallons/cfm. This protects the compressor and dryers from sudden-demand events and prevents false loading.
Efficient dryers can be installed.
The drying technology that offers the maximum allowable pressure dew point must be used.
The use of demand flow controllers is crucial.
The higher the pressure delivered to the plant, the higher the artificial demand and, therefore, higher the leakage losses. Demand flow controllers help isolate the supply side from the demand side and provide a steady flow of low pressure air.
The replacement of timer drains with float type traps.
Timers tend to discharge compressed air wastefully along with condensate. Float type traps discharge condensate alone once they fill up with water, avoiding the loss of compressed air.
A compressed air audit helps optimize productivity, reduce operating costs and improve quality. At ELGi, we believe in a systems thinking approach to help our clients deliver the best. Our team of industry-leading personnel conduct complimentary air audits, enabling our clients to save millions of dollars in energy costs annually. ELGi air audits range from full system audits to specific procedures, such as leak detection and power and flow rate measurements.