Consultant - Screw compressorA 3-STEP APPROACH TO MAINTAIN AN AIR COMPRESSOR FOR OPTIMUM PERFORMANCE
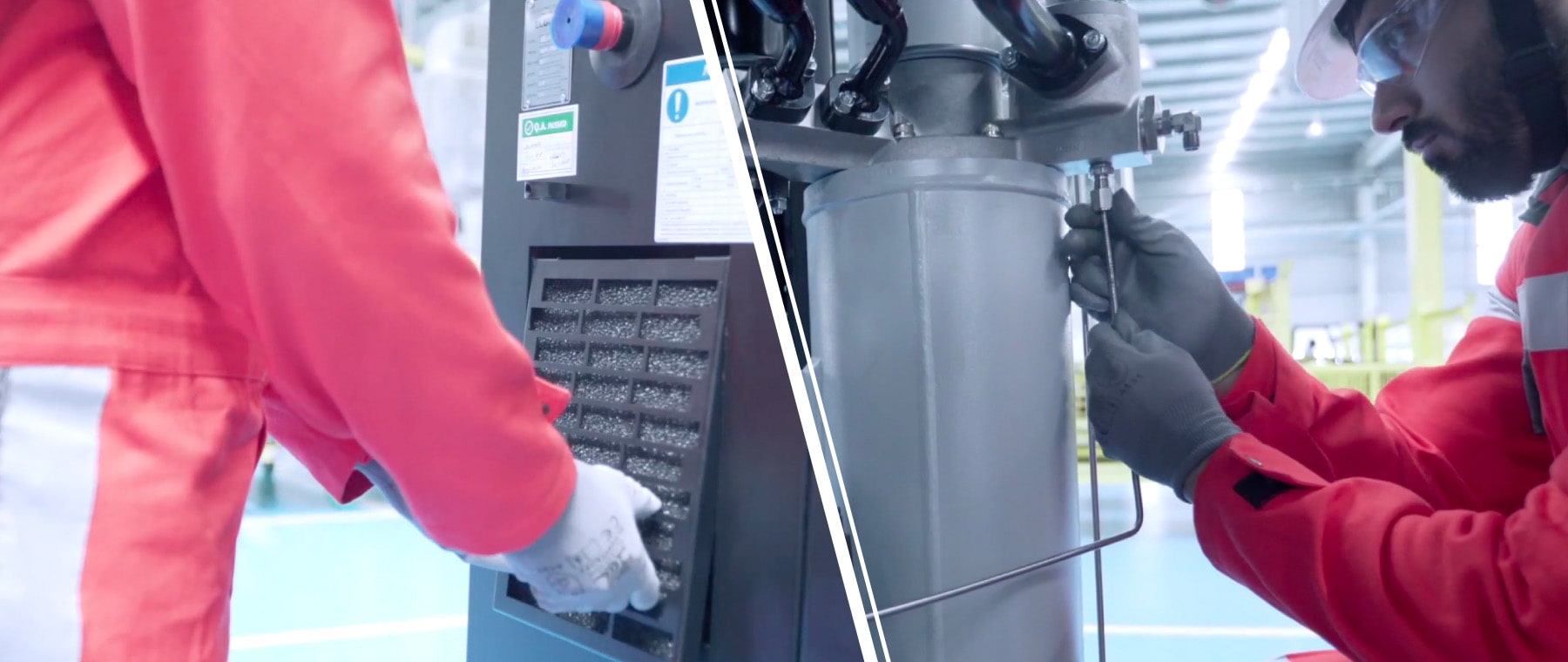
Compressed air is considered to be the fourth most important utility after electricity, water, and natural gas. However, it is also the most expensive of the four. This is why organizations look for efficiency and reliability while looking for air compressors. One way to ensure this is to select the right maintenance plan, to ensure higher productivity and savings.
Types of maintenance:
1. Reactive Maintenance:
Fix the defect after it occurs to restore the air compressor to its normal operating condition.
2. Preventive Maintenance:
Carry out maintenance based on how the air compressor runs over hours or days and eliminate the defect before it occurs. The goal here is to prevent the defect.
Example: Changing oil, filter, separator, and valve kits as per manufacturer recommendations.
3. Predictive maintenance:
Prevent failure by time/condition-based monitoring to plan and schedule regular checks. The goal is to predict failures in advance (based on certain conditions) and resolve them.
Predictive maintenance can be done using conventional methods and IoT Technology.
Furthermore, you can take a look at :
Conventional Methods:
- Health check-up:
Health check-ups are performed at regular intervals to monitor the condition of the components of the air compressor. If any abnormalities are found, a solution will be provided immediately to avoid failure.
Health check-ups include:
- Monitoring the condition of the air filter, oil filter, oil, separator elements, and ventilation
- Checking air and oil leakages at various locations
- Monitoring the inlet and outlet temperatures of air and oil
- Monitoring the condition of electrical contactors, overload relays, transformers, sensors, cables, and PLC
- Checking the functioning of PLC
Checking the functioning of the control valves
Oil sampling:
Oil sampling is a process of collecting a volume of oil from the air compressor for analysis. It helps monitor oil properties, condition of the oil, change in viscosity water content, and identify contamination.
Oil analysis helps understand:
- If the air compressor is running consistently within the correct temperature range
- If there is adequate filtration
If there is any wear and tear of rotors and gears
Shock Pulse Method:
The Shock Pulse Method is a signal processing technique. It measures the metal impact and rolling noise as found in rolling bearings and gears.
This is a preferred method for predictive maintenance throughout the world.
Rolling element bearings are the most common measurement for shock pulse, but the technique has several other applications such as gear conditioning, compressor conditioning, and others where metal to metal contact takes place.
- Vibration Analysis:
This helps measure the vibration levels of the air compressor. The data from the analysis is then used to evaluate the health of the machine.
IoT Technology:
IoT-enabled devices are fitted in the compressors to acquire operation and performance data from the controller and transmit the encrypted data to a secure cloud server. The air-alert server collects the data, analyses it, and sends alerts to correct any abnormalities.