Consultant - Screw compressor5 BEST PRACTICES TO GET MAXIMUM ROI ON YOUR AIR COMPRESSOR
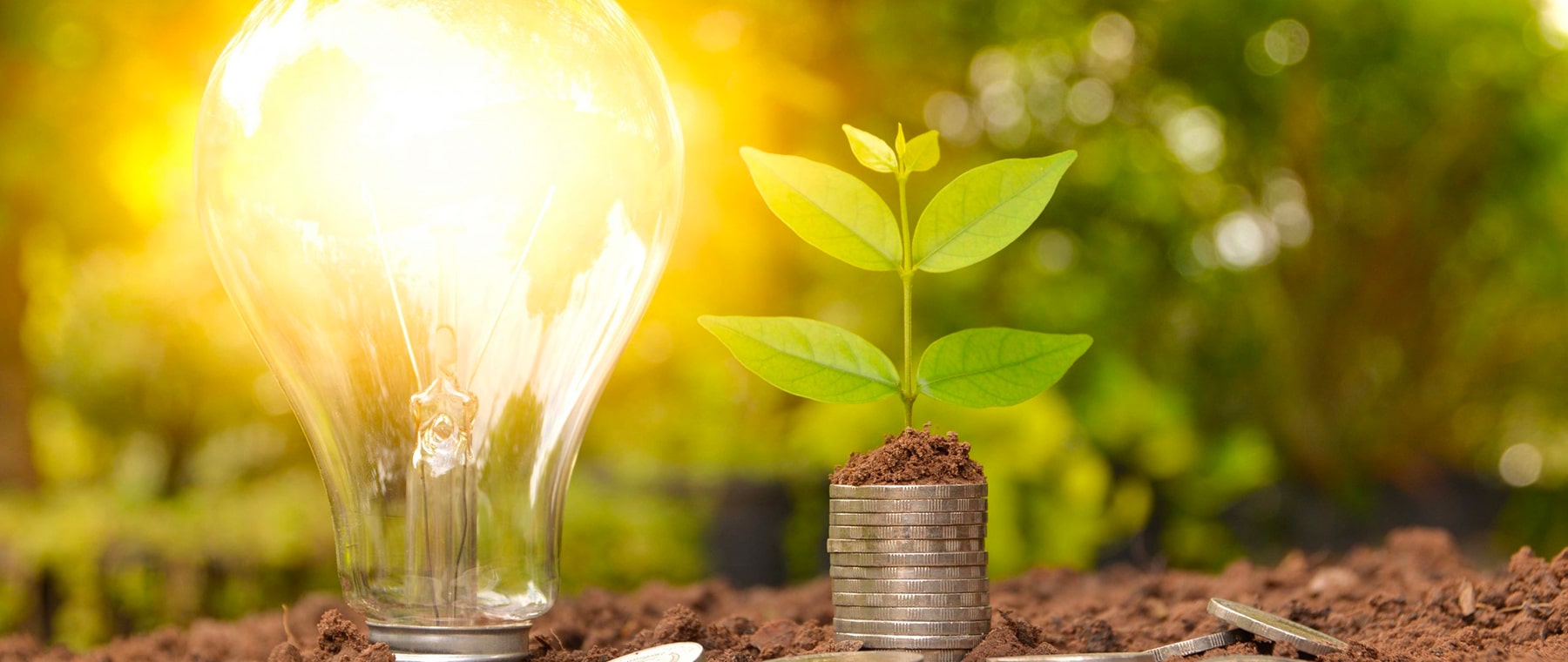
The Evolution of Air Compressors
The use of compressed air spans rudimentary mechanic shops powered by decades-old reciprocating compressors to large scale textile units powered by high volume centrifugal compressors. While the basic technology has remained fairly simple — powered pistons, screws, or impellers compress a volume of atmospheric air to a required pressure — the design and use of compressed air systems have evolved to suit the industry needs.
Compressed air and power consumption
For manufacturers, achieving optimal efficiency is always a challenge as compressed air is inherently inefficient. Fossil fuels are more efficient in getting work done for the same amount of energy. However, compressed air is among the best ways to safely store and use energy. Thus, compressed air has remained a prevalent energy source for industry. Manufacturers have innovated to reduce lifecycle cost, improve reliability, and improve air quality.
The Table below shows the typical lifecycle of a compressor. Nearly 75% of the cost incurred over a ten year period comes from the power consumption.
Here are 5 simple steps that can ensure that your compressed air system brings you maximum ROI during its lifetime:
Step 1: Size up Your Needs
Bigger is not better for compressed air. A screw compressor should continuously “load” or produce air for maximum efficiency. A compressor will continuously load when its air production capacity matches the air requirement. For example, if a compressor produces 500 CFM but the air requirement is only 300 CFM, then the compressor will be in unload condition for a significant portion of time. Screw compressors are inefficient in the unload condition and thus a larger compressor will consume more energy than a right sized compressor for a given air requirement.
The table below illustrates the difference in power consumption between a right sized compressor and one that is too large for the requirement.
To be appropriately sized, customers should demand a sizing audit from manufacturers so that the recommended machine matches the requirement.
Step 2: Match Your Frequency
Right sizing is sufficient for those customers with stable air demand, but how about those customers who have varying demand patterns during the day or those customers who anticipate an increase in manufacturing capacity requiring more air? Variable Frequency Drives (VFDs) can address both situations. A VFD works by reducing the compressor motor's speed to lower flow to match the actual air demand of the customer and thereby consume lower power when compared to a fixed speed machine; thus significantly reducing unload energy consumption. A few manufacturers offer compressors with in-built VFDs while other manufacturers offer systems that can be retrofitted.
The table below illustrates the power savings with a VFD
To evaluate the need for a VFD, customers should demand a sizing audit from manufacturers along with relating a fairly accurate view of upcoming changes in air demand. With this information, manufacturers should provide a lifecycle cost comparison of a VFD solution along with a payback period based on the energy savings.
Managing a Dynamic Air Distribution System
Thus far, the discussion has centered on compressed air generation. Specifically, best practices in selecting a machine for energy efficiency. However, the biggest area for air wastage and thus energy inefficiency is the distribution system. Specifically, the way in which the compressed air is transported and used in the end application.
Step 3: Ensure a Smooth Flow
Line Design
Simply, the shorter the distance from the compressor to the application the better. In addition, minimizing bends and kinks en route to the application, reduces pressure drops and thus improves the efficiency of the system
The diagram below compares an inefficient line design vs an efficient design.
Line Material
Plastic, aluminum, and steel are used for piping, with steel and aluminum being the most popular in India. While steel is cheaper than aluminum aluminum offers benefits such as lower weight and corrosion resistance. Compressed air contains trace amounts of oil and water, which can cause line corrosion, which in turn result in pressure drops and thus degrades the efficiency of the system. Also, compressed air lines are dynamic in that they are constantly vibrating owing to the passage of compressed air. Over time, these movements weaken joints and can result in leaks. Leaks lead to higher energy consumption owing to air wastage.
Step 4: Evaluate and Overhaul
Air audits evaluate the efficiency of use of compressed air in an operation. Air audits can identify energy savings from better compressor selection, improved line design, arresting leaks, and optimizing usage. Compressor manufacturers and independent air audits are capable of conducting air audits. While methods vary, an air audit expert will use flow meters and leak detection devices to evaluate an operation's air usage. Typically, they will spend sufficient time to gain a representative understanding of varying demand conditions. Following the analysis, they will issue a report with a summary of the potential savings along with recommended changes and associated costs to realize the savings. While compressor selection, line design, and line monitoring have been discussed, air auditors will also review the nature of use. For instance, operators in compressed air intensive operations such as textiles will often use a higher than required pressure to operate their machinery. An air auditor might test these machines at lower pressures, and if there is no disruption, the mill operators can continue to operate at a lower pressure, thereby enjoying energy savings. In addition, an air auditor may also recommend against using compressors for energy wasting applications such as cleaning.
The report below is an example of a summary air audit report that shows a textile operation's before and after energy cost following an air audit.
Step 5: Do a Regular Check-Up
Setting up and sustaining an efficient compressed air system requires a monitoring process. Following intelligent compressor selection and delivery design, customers should assign an in-house air expert who is sufficiently trained to monitor the operation's compressed air usage. Specifically, the expert should work with the compressor manufacturer or an independent air auditor to periodically review the company's air usage to identify areas for improvement.